When considering history altering events in the energy sector, few can rival the seismic impact of the oil rush ignited by Edwin Drake's pioneering commercial oil rig in 1859. The oil well produced roughly 25 barrels (one barrel is 42 gallons) of oil per day; but by 1872 using techniques pioneered by Drake, the surrounding area was producing nearly 16,000 barrels of oil per day. Oil boom towns sprung up, fortunes were made and lost, and the petroleum industry was born.
Of course, there were winners and losers in the transition to petroleum. For example, the nascent oil industry rapidly replaced the whale oil industry; providing kerosene for lamps at a much lower cost. Not so good for the whale oil industry, but unanimously supported by the whales! The concern over climate change is now causing many to rethink the role of fossil fuels as the energy source that should drive our future. However, if properly planned and funded, today’s transition to clean energy can be a win for society, the petrochemical industry, and energy producers. Enter the Hydrogen Rush.
In 2021, DOE Secretary of Energy Jennifer Granholm launched the “Hydrogen Energy Earthshot to Accelerate Breakthroughs Toward a Net-Zero Economy.” Reminiscent of NASA’s inspirational “moonshot” mission, the program sets the ambitious goal of reducing the cost of hydrogen production to $1/kg by the end of this decade. Achieving this cost target would be as transformative as the oil rush of the early 1900’s. Recall that low-cost oil came first and the energy transition followed. To date, the largest role for hydrogen has been ammonia production for fertilizers. The next largest roles have been refrigerants, petroleum refining, methanol production and other applications (e.g., food industry, metalworking, welding, electronics manufacturing and medical). Providing a source of carbon-free hydrogen for these industrial users would be a major step towards decarbonization. The key challenge is the ability to produce carbon-free hydrogen with high reliability at commercial scales.
Since 2014, NuScale Power has been investigating innovative approaches to commercial scale carbon-free hydrogen production as part of its road map for NuScale-powered plant integrated energy systems. Consider the largest class of oil wells each producing >12,800 barrels of crude oil per day. Roughly 51% of this crude oil will eventually be refined to produce approximately 276,000 gallons of gasoline. In terms of energy content, this would be equivalent to 276 metric tons of hydrogen (H2).
A NuScale-powered plant consisting of 6 small modular reactors coupled to a hydrogen production system would produce 250-270 MT of H2 per day; the energy equivalent of the amount of gasoline that could be refined from the largest class of oil wells in the U.S. It could produce enough hydrogen annually to supply nearly 5 million fuel cell passenger cars or 196,000 long-haul fuel cell trucks. The off-grid capability of this plant makes it ideal for placement in the proximity of a dedicated industrial hydrogen user such as a mid-size ammonia plant (~1350 MT of ammonia per day).
Most importantly, the hydrogen is generated without producing carbon emissions. Because nuclear power inherently provides carbon-free electricity and steam, has a very small footprint, and very high-capacity factors, it is ideally suited for commercial scale production of hydrogen. Coupling a nuclear plant to a state-of-the-art system of solid oxide electrolysis cells (SOEC) can readily produce commercial scale quantities of hydrogen in a carbon-free and highly reliable and efficient manner.
Two models for nuclear generated hydrogen production are gradually evolving. The first is a centralized hub in which an existing large scale nuclear plant is coupled to an SOEC or low temperature electrolysis system to produce and store hydrogen for distribution to nearby industrial users of hydrogen such as a cluster of steel refining mills. The second model is a distributed hub using small modular reactors. The NuScale-powered plant has a small land mass, ~40 acres, is approved for off-grid operation and has a site boundary emergency planning zone which allows proximity to the industrial user. This eliminates hydrogen transportation costs and provides the industrial user a dedicated source of H2, dioxygen (O2), electricity and process heat with high-capacity factors. Flexible operation and load following provides transition from power to H2 production and allows for integration with renewables.
Climate change is driving industry to a major energy transition, much like what followed the oil rush of the late 1800’s. Are we seeing the beginning of a Hydrogen Rush?
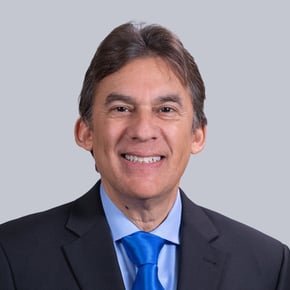